Epoxy Flooring: The Future of Residential Flooring in Australia
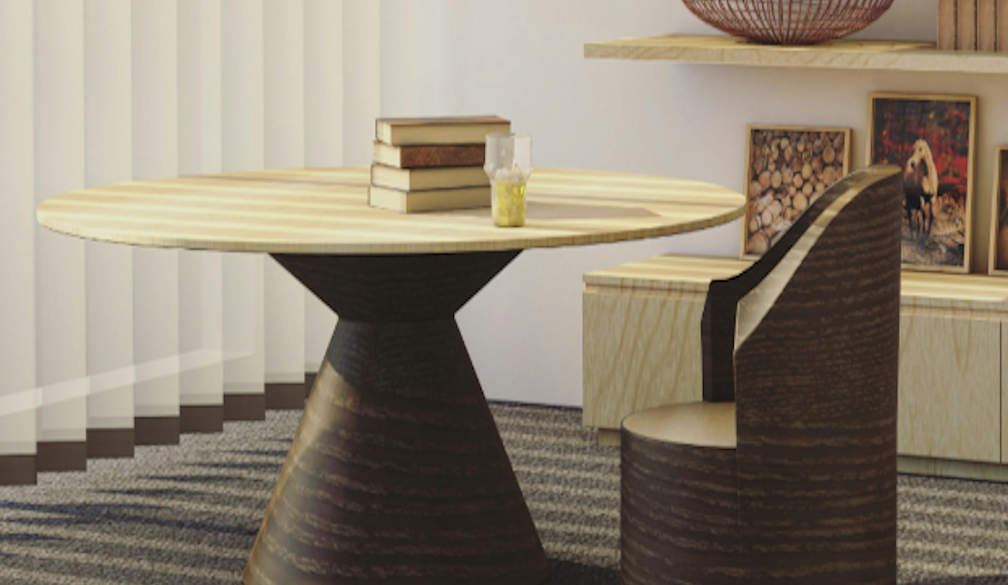
Epoxy flooring is rapidly emerging as the top flooring solution for Australian homeowners. Traditionally associated with industrial and commercial spaces, epoxy coatings are now becoming a popular choice for residential interiors due to their exceptional durability, low maintenance, cost-effectiveness, and design flexibility. In this article, we explore why epoxy flooring is poised to become the future of residential flooring in Australia. We’ll compare it with tiles, vinyl, and timber flooring and evaluate its relevance across four key Australian cities: Sydney, Melbourne, Brisbane, and Perth.
-
Durability and Performance
Epoxy flooring stands out for its durability. Unlike traditional timber that dents and warps or tiles that crack and lose grout integrity, epoxy forms a hard, continuous surface that resists impact, abrasion, and chemical spills. In homes with children, pets, or high foot traffic, epoxy flooring maintains its appearance for years.
Timber, though attractive, is vulnerable to scratches, moisture, and termites. Vinyl, while resilient, tends to wear out in high-use areas and may tear or bubble over time. Tiles, although durable, are prone to chipping and have grout lines that trap dirt and mold. Epoxy, being seamless, addresses these problems by offering a fully sealed, impervious layer over the substrate.
With a lifespan of up to 20 years or more when installed and maintained properly, epoxy is an excellent long-term investment. Its resistance to stains, heat, and moisture makes it suitable for all rooms, including kitchens, bathrooms, and laundries.
-
Maintenance and Hygiene
One of the most significant advantages of epoxy flooring is how little maintenance it requires. A simple mop or sweep is usually enough to keep it looking new. Its non-porous surface does not harbor dust, bacteria, or allergens, making it an ideal option for households with allergy sufferers or pets.
Unlike timber, epoxy does not require refinishing, sealing, or sanding. It won’t absorb spills, making it easier to clean than vinyl and far more sanitary than tile grout. For homeowners who want a stress-free, hygienic floor, epoxy delivers unmatched ease.
-
Cost and Lifecycle Value
The cost of installing epoxy flooring varies based on the finish and the complexity of the application. Basic epoxy finishes start from $30–$35 per square meter, while more decorative or high-performance systems like flake or metallic epoxy can cost up to $100 per square meter.
When compared with tiles (average $90–$125 per square meter) or hardwood timber (often $100+ per square meter), epoxy is far more affordable upfront and over the floor’s lifetime. Vinyl flooring falls within a similar price range to epoxy but lacks its longevity. Additionally, epoxy’s long service life and low maintenance requirements contribute to reduced lifetime costs, offering better return on investment.
-
Aesthetic Versatility
Modern epoxy floors are no longer limited to solid grey industrial looks. Today, homeowners can choose from a wide range of colors, textures, and decorative effects:
- Metallic epoxy creates a marbled or pearlescent look ideal for modern interiors.
- Flake epoxy systems offer a speckled, granite-like appearance with added slip resistance.
- Quartz and terrazzo finishes add decorative flair to entryways and living areas.
- 3D epoxy can produce stunning visual effects, such as ocean or forest themes.
With epoxy, design options are virtually limitless. It can be tailored to match any décor style—from ultra-modern and minimalist to earthy and rustic. Unlike tiles, which are limited by batch designs, or timber, which follows natural grain patterns, epoxy is customizable on-site and can be updated with a new coat as tastes evolve.
-
Environmental Impact
While epoxy is a synthetic resin, its environmental footprint can be offset by its long life and low material usage. Its durability reduces the need for frequent replacements, which in turn lowers waste. It can often be applied over existing concrete or tiles, minimizing demolition waste.
Low-VOC (volatile organic compound) epoxy products are now widely available, making them safer for indoor air quality. Once cured, epoxy emits no fumes, and cleaning requires no harsh chemicals. This makes it suitable for eco-conscious homeowners seeking a long-lasting, sustainable solution.
-
Installation and Practical Considerations
Professional installation is essential for ensuring the performance and longevity of epoxy flooring. The surface must be properly prepared, often by diamond grinding, and the resin components mixed and applied with precision. Curing typically takes 24–72 hours.
Because epoxy adheres best to concrete, it’s commonly used on ground floors or as epoxy floors for garages. However, with proper underlay, it can also be applied over timber or existing tiles. Its minimal thickness ensures smooth transitions between rooms without altering floor levels.
Slip resistance can be customized by incorporating aggregates into the topcoat. Anti-slip finishes are especially useful in kitchens, bathrooms, and outdoor areas. For UV-exposed areas like patios, UV-stable topcoats are used to prevent yellowing.
-
City-Specific Applications in Australia
Sydney: With a humid subtropical climate, Sydney homes benefit from epoxy’s water-resistant and mold-resistant properties. In coastal suburbs, epoxy stands up well to salt exposure and is ideal for garages, kitchens, and basements. Its modern aesthetic also aligns with the city’s architectural trends.
Melbourne: Known for its four-season-in-a-day climate, Melbourne homes require adaptable flooring. Epoxy pairs well with underfloor heating systems, providing comfort during winter. It also handles the city's high humidity in summer. In inner-city renovations and contemporary builds, epoxy’s modern finish is increasingly favored.
Brisbane: In Brisbane’s tropical climate, epoxy’s resistance to humidity, mold, and pests is invaluable. Its seamless finish is ideal for indoor-outdoor transitions in open-plan homes. With high rainfall and potential for minor flooding, epoxy provides a waterproof solution for ground-level rooms and garages.
Perth: Perth’s dry heat and high UV exposure require flooring that won’t degrade or fade. UV-stable epoxy coatings are ideal for this environment. Epoxy is also dust-resistant, making it suitable for homes in outer suburbs affected by windblown dust. Its light-reflective finish enhances natural light in open homes.
-
Epoxy vs Traditional Flooring Materials
Feature |
Epoxy |
Timber |
Tiles |
Vinyl |
Durability |
Excellent |
Moderate |
Good |
Fair |
Maintenance |
Low |
High |
Moderate |
Low |
Lifespan |
15–20+ yrs |
10–20 yrs |
10–15 yrs |
8–12 yrs |
Cost |
$$ |
$$$ |
$$$ |
$$ |
Custom Design |
High |
Low |
Medium |
Medium |
Water Resistance |
Excellent |
Poor |
Good |
Good |
Eco-friendliness |
Moderate |
Good (if FSC) |
Moderate |
Low |
This comparison shows that while timber and tiles have their place, epoxy delivers a more balanced, future-proof solution in terms of resilience, customization, and value.
Conclusion
For Australian homeowners seeking a durable, hygienic, low-maintenance, and visually striking flooring solution, epoxy flooring offers unmatched benefits. Its adaptability to climate, style preferences, and modern living needs makes it a top contender across diverse regions—from coastal Sydney to sunny Perth.
Epoxy flooring’s seamless, waterproof finish, custom design options, and minimal upkeep make it an ideal choice for families, renovators, and new builds alike. As more Australians discover its advantages and more installers become available nationwide, epoxy is poised to become the standard in residential flooring for the decades ahead.
Whether you’re renovating a classic home or building a modern masterpiece, epoxy flooring offers the strength, style, and sustainability to support everyday living—now and into the future.